Mecanum Drive Train
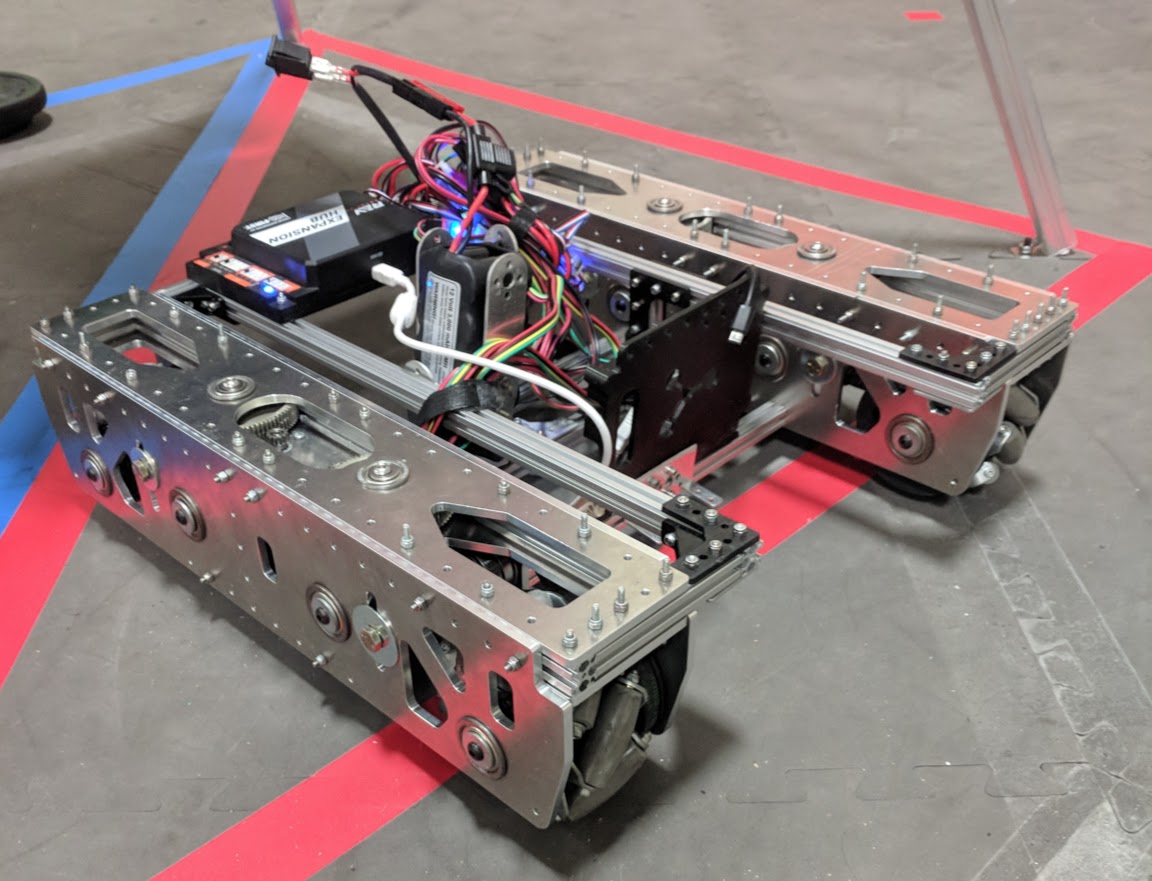
Introduction
Starting as a passion project over the FTC offseason in summer 2018, this design eventually became the drive train FTC 7842 used in the 2018-2019 season. It consisted of four independent 3-stage gearboxes, with the second stage using bevel gears. The bevel gears improved the packaging of the drive train by allowing the motors to be mounted within the drive sides, leaving a large, continuous space through the middle of the drive train. This project was my first thorough introduction to optimizing power transmission design for efficiency, and it was completed through a local machine shop, which taught me the fundamentals of designing for manufacturing.

Goals
The primary goal for this project was to maximize the distance between the drive “pods” by relocating the motors into those pods. This meant that the area between the pods was continuous, with no motors that had to be designed around. Additionally, this drive train aimed to be as well-balanced as possible, because mecanum wheels are somewhat sensitive to an uneven mass distribution, which can compromise the lateral motion and cause curving motion. Finally, the target top speed of the drive train was 5ft/s, which meant that, with acceleration and deceleration phases, the 12ft field could be crossed within a few seconds.
Lessons Learned
Gearbox design and efficiency, as well as applied experience with DFM techniques, were the biggest lessons from this project. Learning to deal with tolerance stackup in gearboxes to avoid lash-based precision issues was a crucial lesson for future engineering projects, and the foundational DFM concepts I learned while working with a local machine shop to manufacture parts for the drive train will be useful for the entirety of my mechanical engineering career.