FIRST Tech Challenge 2019-2020 Robot Design
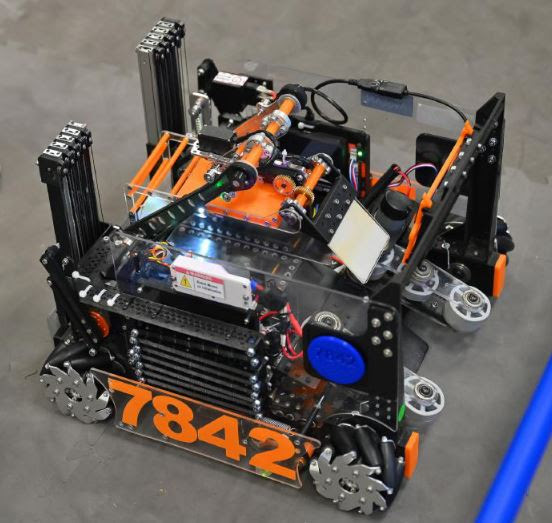
Introduction
In the 2019-2020 FIRST Tech Challenge season, I was the only mechanical designer on my team, FTC 7842. As such, I was responsible for designing all of the mechanical systems in SolidWorks, and I did so by interpreting prototyping results for some mechanisms from other members of the team, while I directly designed and handled some other systems. This was by far the most complex CAD model I had worked on up to this point, and it was far more detailed than previous years'. Every system was fully modeled in SolidWorks before being manufactured in-house on a hobby CNC router or a manual lathe, and then multiple team members contributed to the assembly of the systems.


Goals
For this challenge, the team wanted to be able to grab and control elements while at top speed, and we wanted to be able to transfer them into the scoring area through the back of the robot. This meant that scoring cycles could be completed without fully rotating the drive train, thereby substantially improving cycle times. Additionally, we wanted to be able to cross the field very quickly, which necessitated that the robot be kept light for improved acceleration characteristics.
Lessons Learned
This project taught me about designing for additively manufactured components, which were used extensively on this robot. In particular, we noted a consistent trend in the failure modes of these parts, where FDM-produced parts bearing torsional loads would frequently shear between layer lines. To combat this, future torque-transferring parts were reinforced with metal screws wherever possible, which kept the layers in compression and would act as a failsafe method of torque transfer if the layers did shear. This project was also a great lesson in mechanical packaging because certain areas of the robot were very dense and required unique solutions to make everything fit. Finally, rigorous design and performance tracking processes were implemented throughout the team this season, which allowed us to compare our initial goals to current progress and make changes accordingly, as well as ensure that the entirety of the team was up to speed on the status of every component on the robot.