Motor Torque Measuring Stand
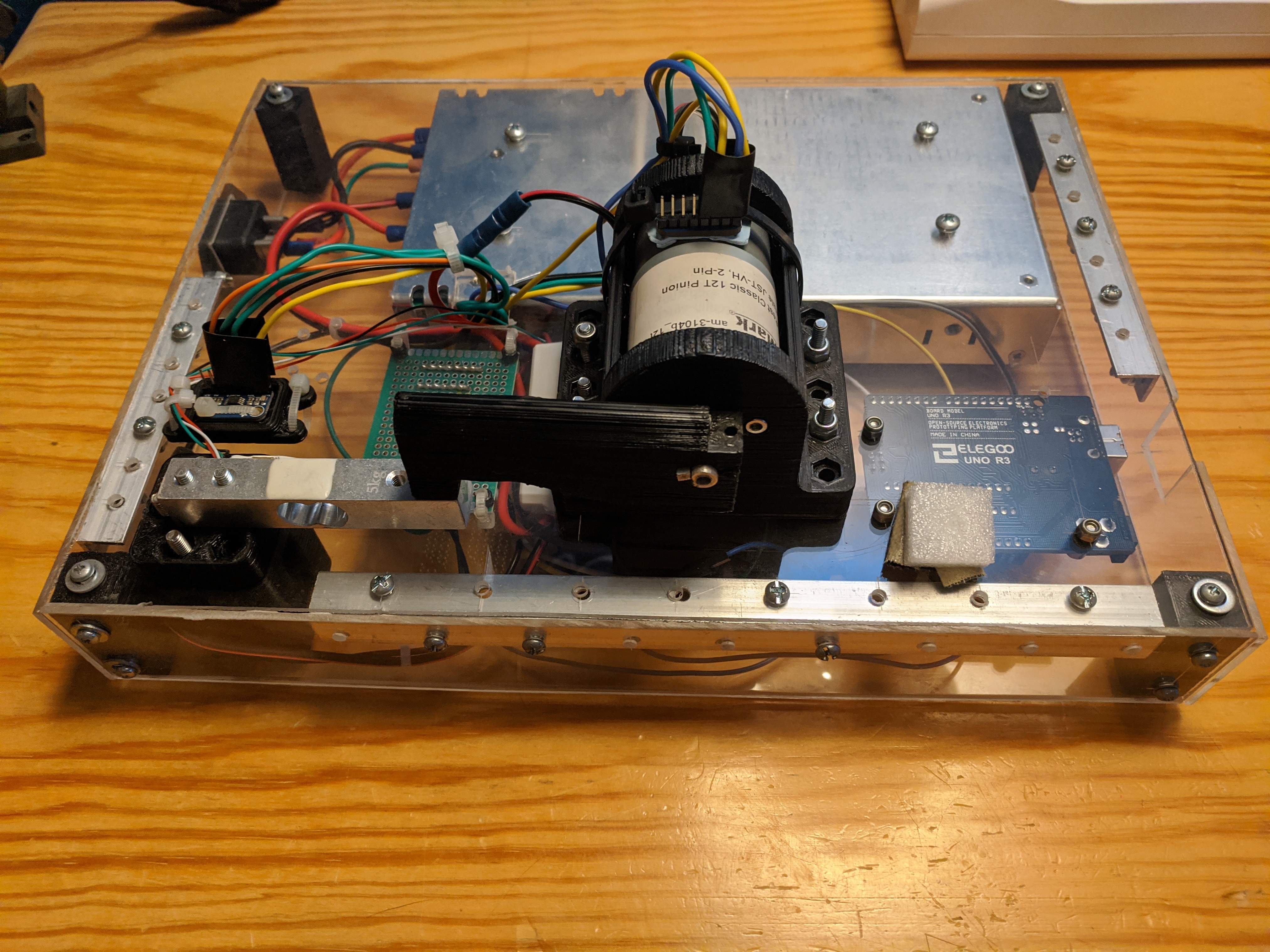
Introduction
This project was completed as a semester-long group project for UAH’s Principles of Measurements and Instrumentation course, which surveyed measurement methods and devices and discussed topics like sensor accuracy, precision, data acquisition and processing. A major component of this course is the group project (done in teams of 4 to 6 people), which is an open-ended project beginning with an ideation phase before writing a formal proposal, including an estimated budget, timeline, and what the group intends to measure and against what variables. There are only a handful of firm requirements for this project, including sensor calibration and a system uncertainty analysis, but beyond those requirements, the project direction is up to the individual groups. In the case of my group, I suggested investigating whether the magnitude of temperature rise of an inexpensive brushed DC motor’s casing during a locked-rotor condition was linear with respect to its applied voltage, and whether the torque derates linearly with the current motor temperature. Torque vs. temperature curves are often provided for more expensive motors by the manufacturer, but for cheaper hobby-grade motors, no such information is provided, but the information can still be beneficial to designers in those hobby applications. I went on to lead the group’s development efforts for this project, and I was solely responsible for the mechanical design, component fabrication and writing the data acquisition system, while the group jointly contributed to part sourcing, report writing, assembly, and sensor calibration.
Design Process
One of the major constraining factors for this project was cost because the intent of the course project was to be a low-cost, open-ended opportunity for students to work in groups on self-defined objectives. As such, many parts were chosen - such as the motor, some electrical components, and others - because members of the group already had them from previous projects. The rest of the project was assembled using COTS components alongside 3D printed parts and custom acrylic housing panels. The system was designed in Solid Edge, the CAD package offered by the university, and while certain aspects were quite straightforward, the load cell mounting assembly, the arm that mounted to the motor shaft to apply load to the load cell, and the housing around this area all needed to deflect only minimal amounts to ensure accurate results. To achieve this, I used Solid Edge’s integrated force simulation tools, which aren’t as robust as dedicted FEA programs but were more than adequate for a project of this complexity, to simulate the designs for the 3D printed parts contained within the aforementioned assemblies, and then I iterated on those designs by adding or removing material to maximize stiffness and minimize material use, based on where the stresses were concentrated in the parts.

Manufacturing and Assembly
Initially, the acrylic panels for the housing were intended to be laser cut in UAH’s MAE department’s machine shop, but it was inoperable when we were manufacturing the panels, so I instead created drawings outlining the essential dimensions (hole patterns, shape, etc) of the parts and scribed those locations onto the acrylic panels using an old pair of calipers. Then, I used a springloaded center punch (on a low setting to avoid cracking the acrylic) to positively mark hole locations before drilling them out with a hand drill using progressively larger drill bits. A hand drill (and the cautious drill bit size step up) was chosen to avoid cracking the acrylic because it is harder to modulate pressure and speed with a drill press as compared to a hand drill, and the lost accuracy was a worthwhile tradeoff for this application. As for the 3D printed parts, those were printed on my personal 3D printer (as built in another project in my portfolio), which was the plan from the outset.
Assembly, including sensor calibration, was done jointly by the group over a few days, beginning with calibration in an MAE lab. Using the lab allowed us to calibrate our sensors against NIST-traceable sensors and calibration equipment like calibrated masses and thermocouples. This data was collected and compared to the data from our sensors - or in the case of the calibrated masses, we measured the output resistance of our load cell at many known loadings - and simple linear models were generated to convert the raw sensor data to the calibrated output. After sensor calibration, most of the rest of the assembly process was straightforward.
Challenges
There were a few major challenges with this project, which will be individually outlined in separate paragraphs below. These include mounting the torque arm to the motor shaft, electrical issues causing instability in the system performance, and a sensor failure.
At the time, none of our group members had completed all of the training necessary to access machining tools like the lathes and mills in the MAE machine shop, so we had to devise a low-accuracy solution to mounting the torque arm to the motor shaft. Normally, a pressfit would be the primary way to mate a component to this kind of motor shaft, but we were not able to hold tight enough tolerances to create such a pressfit feature in a part. As such, I made a small aluminum tube with a flat on one side of the outer diameter and pressed in a rectangular aluminum piece to “key” the tube to the torque arm. Then, the aluminum tube was bonded to the motor shaft using a motor-focused Loctite adhesive, which enabled robust torque transfer from the motor to the torque arm. This wasn’t the most elegant solution, but it satisfied our requirements and was fairly low-cost as well, so it was deemed “good enough”, although a more robust (and removable) method would need to be devised if we ever wanted to test more than one motor with this system.
Another major issue was a loose pin on our 5V bus, occasionally killing power to every device wired into it. This included the motor controller, whose logic operated on 5V. When this happened, the motor would violently backdrive the torque arm into the acrylic panel and stall against it until 12V power (for the motor) was removed. Ultimately, our solution was to tape all of the connections (ideally strain relief would have been implemented, but this issue was discovered late into the project’s life cycle) and add a thick foam pad to the location where the torque arm would contact the acrylic plate, which dampened the blows somewhat.
Finally, one of the biggest challenges the group faced occurred shortly after assembly was complete, when the I2C bus (which we used for our temperature sensors and a voltage sensor) seemed to be permanently stuck in a low state, resulting in all three sensors failing to initilize or record any data. After much debugging and diagnosing, we realized that the voltage sensor was pulling the rest of the I2C bus low and seemed to have failed, whereas the other two sensors were operating normally when the voltage sensor was removed from the bus. After discussing the incident more, we realized that the cause of failure was likely when the motor was briefly spun up continuously while testing during assembly. The sensor’s manufacturer recommended using a flyback diode for inductive loads, but we omitted this part because we didn’t expect our motor to ever continuously spin (only stall into the load cell). This likely would’ve been fine for the stall-only condition, but that simple spin up-spin down cycle was enough to brick the sensor, and the scope of the project was narrowed to use PWM duty cycles instead of direct voltage measurements (which is a nonideal compromise because PWM may not represent actual DC behavior at the voltage the signal is approximating and because it assumes that the PWM controller is fairly accurate).
Lessons Learned
While I learned many lessons from this project - such as considering failure mode edge cases that are outside of normal operating parameters, as with the voltage sensor - I think what was most beneficial was managing a team with a diverse array of skills and proficiency levels. It required the group to be vocal about what they were comfortable with and what they were interested in learning, it forced people to ask questions when they were stuck, and it impacted our nominal timelines to a degree that I didn’t expect when we initially drafted the schedule. Despite all of these setbacks and curveballs, the project weathered the storm and I learned a lot about engaging in groups in a simultaneous mentoring and learning dynamic.